ER316 SS MIG WIRE | FEATURES
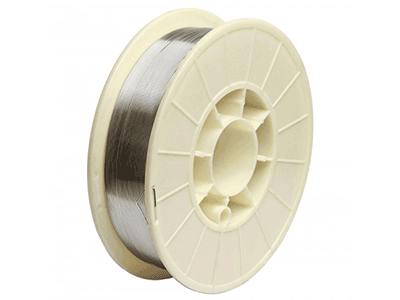
- The nominal composition (wt,-%) of ER316 is 19 Cr, 12.5 Ni, and 2.5 Mo.
- It has been used successfully in certain applications involving special base metals for high-temperature service.
- The presence of molybdenum provides creep resistance at elevated temperatures and pitting resistance in a halide atmosphere.
- Welding process of ER316 SS MIG wire applied to MIG(Metal Inert Gas Welding) or GMAW(Gas Metal Arc Welding).
SPECIFICATION CONFORMANCES
AWS: A5.9/A5.9M: ER316
UNS Number: S31680
BS EN ISO 14343B: SS316
WELDING POSITIONS: F,V,OH,H
TYPICAL APPLICATION
- ER316 SS MIG wire is used for welding Type 316 and similar alloys, such as 316 and 316N.
- Applied to LNG Storage, Cryogenic Vessels and Piping.
Rapid corrosion of ER316 weld metal may occur when the following three factors co-exist:
1. The presence of a continuous or semicontinuous network of ferrite in the weld metal microstructure.
2. A composition balance of the weld metal giving a chromium-to-molybdenum ratio of less than 8.2 to 1.
3. Immersion of the weld metal in a corrosive medium. Attempts to classify the media in which accel- erated corrosion will take place by attack on the ferrite phase have not been entirely successful. Strong oxidizing and mildly reducing environments have been present where a number of corrosion failures were investigated and documented.
WIRE COMPOSITION – As Required As per AWS A5.9/A5.9M
Alloy Type | %C | %Cr | %Ni | %Mo | %Mn | %Si | %P | %S | %Cu | Other |
---|---|---|---|---|---|---|---|---|---|---|
ER316 | 0.08max | 18.0-20.0 | 11.0-14.0 | 2.0-3.0 | 1.0-2.5 | 0.30-0.65 | 0.03max | 0.03max | 0.75 | – |
Typical Results | 0.053 | 19.2 | 12.6 | 2.52 | 1.8 | 0.46 | 0.015 | 0.014 | 0.47 | – |
DIAMETER
INCH | 0.023” | 0.030” | 0.035” | 0.040” | 0.045” | 0.062” |
---|---|---|---|---|---|---|
MM | 0.6 | 0.8 | 0.9 | 1.0 | 1.2 | 1.6 |
Standard Package Dimensions and Weights
Product | Spool Diameter(in) | Spool Diameter(mm) | Nomimal Weight(lbs) | Nominal Weight(kg) |
---|---|---|---|---|
Spools | 4 | 100 | 1-1/2, 2-1/2 | 0.7, 1.1 |
8 | 200 | 10 | 4.5 | |
12 | 300 | 25, 33 | 11.4, 15 | |
14 | 350 | 50 | 22.8 |
*Net weights shall be within ±10% of the nominal weight.
TYPICAL MECHANICAL PROPERTIES (As Welded)
AWS No. | Tensile Strength, min(ksi) | Tensile Strength, min(MPa) | Elongation, min(%) | Heat Treatment |
---|---|---|---|---|
ER316 | 75 | 520 | 30 | None |
Available Diameters MIG with Operating Range in Amps
Diameter(inch) | Diameter(mm) | Amps(A) |
---|---|---|
0.023” | 0.6 | 35 – 70 |
0.030” | 0.8 | 50 – 100 |
0.035” | 0.9 | 160 – 210 |
0.045” | 1.2 | 180 – 250 |
MIG SPOOL DIMENSIONS
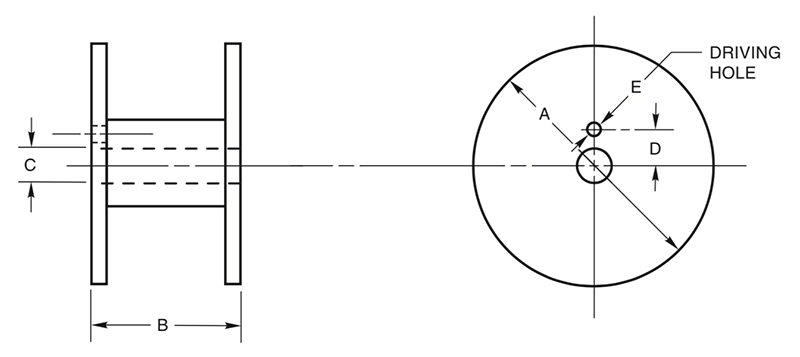
Dimensions of 4, 8 and 12 in [100, 200 and 300 mm] Standard Spools | |||||||||
Type | Spools Details | 4 in [100mm] | 8 in [200mm] | 12 in [300mm] | 14 in [350mm] | ||||
inch | mm | inch | mm | inch | mm | inch | mm | ||
A | Diameter, max | 4.0 | 102 | 8.0 | 203 | 12 | 305 | 14 | 355 |
B | Width Tolerance | 1.75 ±0.03 |
46 +0,-2 |
2.16 ±0.03 |
56 +0,-3 |
4.0 ±0.06 |
103 +0,-3 |
4.0 ±0.06 |
103 +0,-3 |
C | Diameter Tolerance | 0.63 +0.01.-0 |
16 +1,-0 |
2.03 +0.06,-0 |
50.5 +2.5,-0 |
2.03 +0.06,-0 |
50.5 +2.5,-0 |
2.03 +0.06,-0 |
50.5 +2.5,-0 |
D | Diameter between Axes Tolerance | — — |
— — |
1.75 ±0.02 |
44.5 ±0.5 |
1.75 ±0.02 |
44.5 ±0.5 |
1.75 ±0.02 |
44.5 ±0.5 |
E | Diameter Tolerance | — — |
— — |
0.44 +0,-0.06 |
10 +1,-0 |
0.44 +0,-0.06 |
10 +1,-0 |
0.44 +0,-0.06 |
10 +1,-0 |