Flux-cored arc welding (FCAW) is an arc welding process that uses an arc between a continuous filler wire and the weld pool. The process is used with shielding gas from a flux contained within the tubular electrode with or without additional shielding from an externally supplied gas, and without the application of pressure. This is a variation of GMAW and is based on the configuration of the electrode.
There are two variations of process. One uses externally supplied shielding gas, and the second relies entirely on shielding gas generated from the disintegration of the flux within the electrode. Of the variation using externally supplied shielding gas, there are two distinct types of electrodes. One is the original flux-cored type electrode, where the materials contained within the tubular electrode are primarily fluxing agents. Another type, known as metal-cored wire, contains alloy elements as well as powdered iron to enhance productivity with a minimum amount of fluxing material. Both flux-cored and metal-cored wires require external gas shielding. This is more logically called cored wire welding and is almost identical to gas metal arc welding, except for the electrode. In some countries, cored wire welding, either flux-cored or metal-cored, is considered a variation of gas metal arc welding.
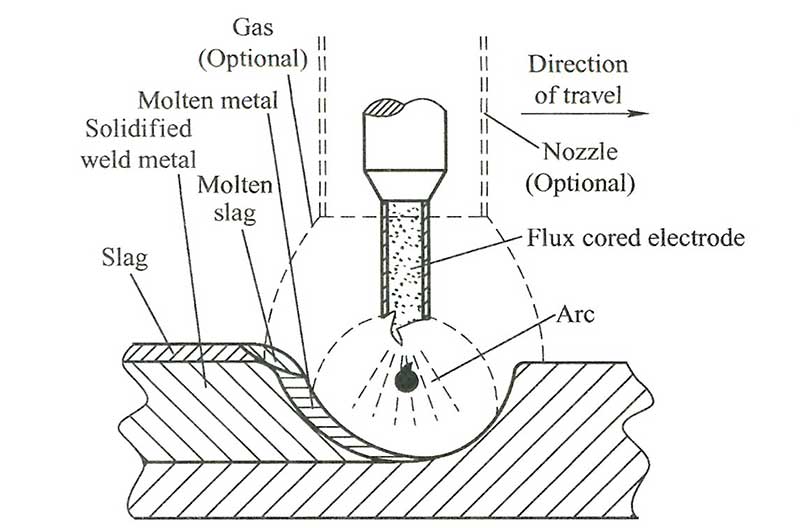
Figure 1 Process diagram for FCAW
The FCAW process (Figure 1 ) utilizes the heat of an arc between a continuously fed consumable cored electrode and the work. The heat of the arc melts the surface of the base metal and the end of the electrode. The metal melted off the electrode is transferred across the arc to the workpiece, where it becomes the deposited weld metal. Shielding is obtained from the disintegration of ingredients contained within the flux-cored electrode. Additional shielding is obtained from an envelope of gas supplied through a nozzle to the arc area. ^ Ingredients within the electrode produce gas for shielding and also provide deoxidizers, ionizers, purifying agents, and in some cases alloying elements. These ingredients form a glasslike slag, which is lighter in weight than the deposited weld metal, and floats on the surface of the weld as a protective cover. The electrode is fed into the arc automatically, from a coil. The arc is maintained automatically, and travel can be manual or by machine.
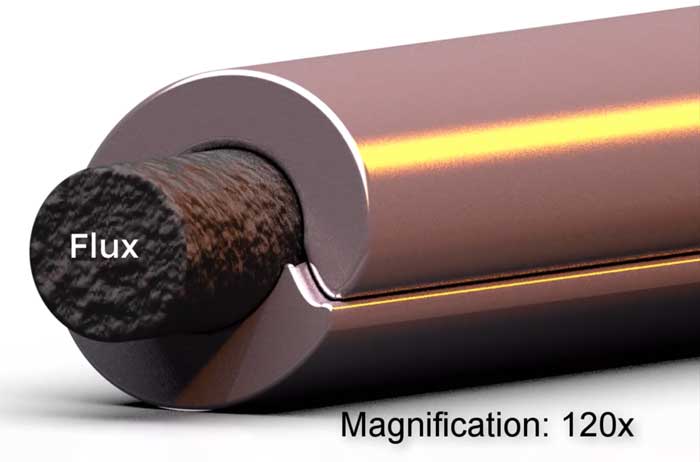
Magnification for section of flux-cored
The electrodes used for flux-cored arc welding provide the filler metal to the weld puddle and shielding for the arc. Shielding is required for sane electrode types. The purpose of the shielding gas is to provide protection from the atmosphere to the arc and molten weld puddle. The chemical composition of the electrode wire and flux core, in combination with the shielding gas, will determine the weld metal composition and mechanical properties of the weld.
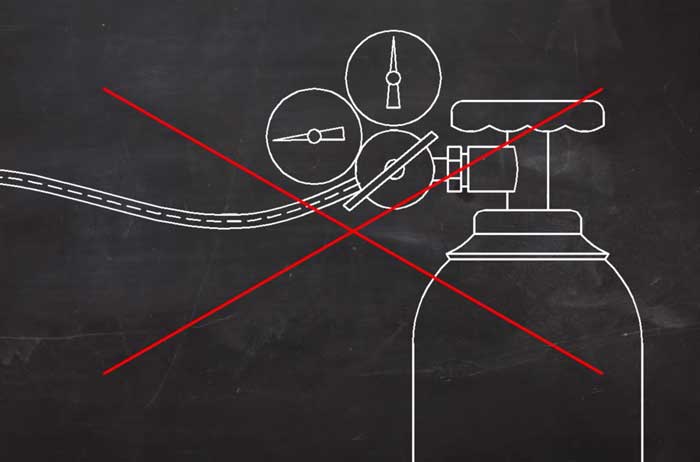
The FCAW process introduced in the early 1950s is an outgrowth of the GMAW process. FCAW has many advantages over the manual SMAW process. It also provides advantages over submerged arc welding and the GMAW processes. Simply stated, the FCAW process provides high-quality weld metal at lower cost with less effort on the part of the welder than SMAW. It is more forgiving than GMAW and is more flexible and adaptable than submerged arc welding.
This process is becoming increasingly popular. It is widely used on medium thickness steel fabricating work, where the fine wire GMAW process would not apply and where the fitup is such that submerged arc welding would be unsuitable.
Get Notified of New Articles
Leave your email to get our weekly newsletter.