1.1 The effect of nickel on the performance of stainless steel and its welds The main role of nickel is to promote the formation of austenitic phase, and use it as the dominant phase to produce austenitic stainless steel or austenitic ferritic stainless steel. Since the austenite phase region can expand greatly after sufficient nickel is added, the austenite remains stable up to room temperature or lower. Although there is evidence that nickel can affect the kinetics of the precipitation reaction in the alloy, nickel is not a strong carbide-forming element and does not promote the formation of intermetallic compounds. There is also some evidence that nickel improves general corrosion resistance in ferritic alloy steels, especially in the presence of sulfuric acid in a reducing atmosphere. However, nickel is associated with reduced resistance to stress corrosion cracking (SCC). Copson’s work clearly shows that the addition of nickel to Fe20Cr alloy steel reduces the ability of the steel to resist SCC in aggressive chlorine-containing environments. The well-known Copson curve shows that the alloy steel has the lowest resistance to SCC in the range of 8% to 12% of Ni content, and whether it increases or decreases the nickel content outside this composition range will increase the resistance to SCC. Nickel is a good solid solution strengthening element and is most beneficial in improving the toughness of martensitic and ferritic stainless steels. Adding Ni in a mass fraction of no more than 2% to a high chromium ferritic stainless steel can significantly reduce the ductile brittle fracture transition temperature (DBTT) of the steel.
In short, nickel is a strong austenite forming element, the main alloying element of stainless steel, and an indispensable alloying element for some types of stainless steel. Nickel is an element that expands the austenite phase region. As the amount of nickel increases, the temperature at which austenite transitions to ferrite decreases to 900-350 ° C. During rapid cooling, the austenite structure is maintained at lower temperatures, even at room temperature. Since the transformation of austenite to ferrite is completely suppressed, this steel cannot be hardened by phase transformation. Austenite is non-magnetic and has no brittle phase in the FeNi system. In the NiCr phase diagram, a eutectic reaction occurs when the amount of nickel is 48%. A γ phase is formed on the nickel side and an α phase is formed on the chromium side. This has an important impact on the performance of nickel-based materials with nickel content greater than 50%. There is no σ phase in the NiCr phase diagram, but there is a σ phase in the FeCrNi ternary phase diagram, as shown in FIG. 14.
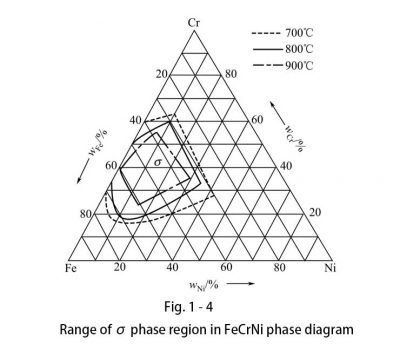
1.2 Effect of Manganese on Properties of Stainless Steel and Welds
Manganese is added to virtually every steel. Historically, manganese was added to prevent hot brittleness during casting, which is caused by the formation of solidification cracks due to the formation of iron-sulfur low melting eutectic components. Because manganese can bind to sulfur more easily than iron, adding enough manganese can form stable manganese sulfide (MnS), which effectively eliminates the problem of hot brittleness.
Manganese is a relatively weak austenite-forming element. Its degree of action is related to its content and nickel content, but it has the effect of stabilizing austenite. In the iron-manganese phase diagram, Mn can expand the γ phase region and shift the γ → α transition to a low temperature. As a result, the austenite is stable at room temperature. The effect of manganese has two aspects. One is to prevent hot cracks in the full austenitic weld and the other is to increase the solubility of nitrogen. This is the theoretical basis for the development of high nitrogen austenitic steels, as shown in Figure 15. . In stainless steel, manganese remains in the steel as a deoxidizing element. The general manganese content of CrNi austenitic stainless steel does not exceed 2%, the manganese content of martensitic and ferritic stainless steel does not exceed 1%, and high purity ferrite. The content of manganese in stainless steel does not exceed 0.4%. As an alloying element, it is only used in nickel-saving austenitic stainless steel, high-strength high-nitrogen austenitic stainless steel, and α + γ duplex stainless steel. In high nitrogen and high interstitial element (C + N) austenitic stainless steel, the amount of manganese is up to 20%, and it can also be up to 5% in duplex steel. In general, manganese has little effect on the mechanical properties of stainless steel, has some solid solution strengthening effects, and does not have embrittlement effects.
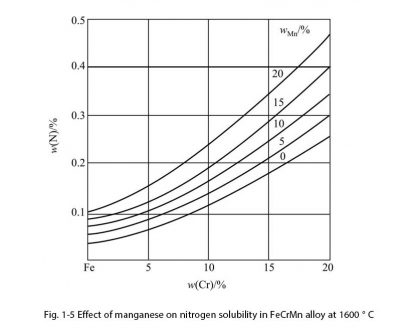
1.3 Effect of carbon on properties of stainless steel and weld metal
Carbon is contained in all steels, but unlike CMn steels and low-alloy structural steels, stainless steel often requires that the mass fraction of carbon be controlled below 0.1%. The only exception is martensitic stainless steel, where carbon is critical in the transformation strengthening of this steel.
Carbon plays a role in strengthening interstitial atoms in solid solutions, especially at high temperatures. In most stainless steels, carbon and other elements form carbides. When chromium-rich M23C6 type carbides are formed, the corrosion resistance is reduced. To this end, low-carbon (L-type) stainless steel has been produced with a carbon mass fraction lower than 0.04%. It is worth noting that M23C6 type carbides contain metal atoms (mainly chromium) that are nearly 4 times the carbon atoms, and the mass of a chromium atom is more than 4 times the mass of carbon atoms, so in terms of mass fraction, M23C6 is formed In the case of type carbides, one part of carbon can remove up to 16 times the mass of chromium from the solid solution.
Carbon is an austenite-forming element and expands the γ-phase region. Its ability to form austenite is 30 times that of nickel. In the FeCrC ternary phase diagram, carbides such as Cr23C6, Cr7C3, Cr3C2, and Fe3C can be formed. The first two may appear in stainless steel. In most cases, (FeCr) 23C6 mixed carbides are formed, represented by M23C6. In chromium-nickel austenitic stainless steel, the carbide phase is mainly composed of M23C6, and M6C type carbides are also present in high-molybdenum and niobium-containing austenitic stainless steels. In stainless steels stabilized with titanium and niobium, MC-type carbides such as NbC, TiC are present. Nickel does not form carbides, and in the nickel-carbon component, carbon always precipitates as graphite. In ordinary stainless steel, carbon forms a compound with chromium first, followed by a compound with iron, and in fact never forms graphite. In stainless steels (such as 188), austenite grains have a good solubility for carbon, but because of the reduced activity of chromium in austenite, the high solubility of carbon in austenite is greatly reduced. Because carbides can be formed at very low carbon levels, the solubility of carbon in austenitic stainless steels is greatly reduced. Carbon also affects the formation of the σ phase. Increasing the carbon content will increase the amount of carbides, and some chromium will become M23C6 high chromium carbides, which will reduce the amount of chromium in the matrix and slow down the precipitation of the σ phase. If carbon forms carbides with titanium or niobium, This inhibition will be reduced. Carbon is inevitable in all types of stainless steel. In martensitic stainless steel, carbon is the most effective and cheapest element to obtain hardenability; in CrNi austenitic stainless steel, carbon is harmful; in duplex stainless steel and ferritic stainless steel, carbon is also harmful It should be reduced as much as possible; however, in high nitrogen CrMnN austenitic stainless steel, carbon and nitrogen can be used to develop high-gap elemental high-strength non-magnetic austenitic stainless steel with the purpose of strength and toughness.
1.4 Effect of Nitrogen on Performance of Stainless Steel and Welds
Nitrogen is present as an impurity in many stainless steels, but nitrogen is intentionally added in some austenitic stainless steels and in all duplex stainless steels. Similar to carbon, nitrogen is a strong solid solution strengthening element; the addition of only 0.15% (mass fraction) can significantly increase the strength of austenitic steel, and its strengthening effect in austenite is particularly significant at low temperatures. Nitrogen also increases strength in duplex stainless steels, but more importantly increases corrosion resistance and crevice corrosion resistance. Some duplex stainless steels contain up to 0.3% (mass fraction) nitrogen. Nitrogen has a low solubility in stainless steel, especially in ferritic stainless steel, and the addition of manganese to austenitic stainless steel can increase the solubility of nitrogen. In ferritic and duplex stainless steels, if nitrogen exceeds its solubility, Cr2N will precipitate in the ferrite phase.
If the proper amount of austenite is not formed in the weld metal and heat affected zone when cooled from a temperature higher than 1100 ° C, precipitation of Cr2N will be observed. Nitrogen, as a very strong element that forms and expands the austenite phase region, has the ability to form austenite equivalent to carbon, about 30 times that of nickel. In austenitic stainless steel, nitrogen increases the stability of austenite, and can also suppress the precipitation of carbides and delay the precipitation of σ phase. Therefore, it has a beneficial effect on the sensitized intergranular corrosion and toughness of steel. In low alloy steel, nitrogen is usually an impurity element, but it can be used as an alloy element in stainless steel. Due to the presence of chromium, nitrogen has a good solubility in steel, so the nitrogen content of stainless steel is higher than that of carbon steel and low alloy steel. As the amount of chromium increases, the solubility of nitrogen in chromium-nickel stainless steels increases rapidly. The solubility of nitrogen can be checked by the number of pores in the steel. The test showed that the maximum nitrogen content without pores rose from 0.20% of 17% Cr to 0.50% of 25% Cr, which was linear with the amount of chromium. Because nitrogen has a much higher solubility in austenitic stainless steel than carbon, nitrogen does not easily form a brittle precipitated phase in austenitic steel. If the solubility of nitrogen exceeds the limit, nitrogen will be precipitated as a Cr2N compound; if carbon is also present, M23C6 type carbides will also be precipitated at the same time. All precipitates that cannot dissolve nitrogen, such as M23C6, molybdenum-containing χ phase, and Laves are equal. Nitrogen can prolong the precipitation time of these phases; while M6C type carbides can dissolve nitrogen, so nitrogen can promote the precipitation of M6C. In FeCrNi, nitrogen and carbon are similar, and both move the σ phase precipitation curve toward a higher amount of chromium. The effect of nitrogen on other intermetallic phases is similar to that of carbon. The solubility of nitrogen in austenite is high, but the solubility in ferrite is low. At about 900 ° C, the solubility is close to 0.01%; as the temperature decreases, the solubility will further decrease. The solubility of nitrogen in steel is related to the composition and structure of the steel. The effects of the amount of chromium, temperature, and structure on the solubility of nitrogen in steel are shown in FIG. 16. Under pressure, as the pressure increases and the amount of chromium increases, the solubility of nitrogen in the steel also increases, as shown in Figure 17.
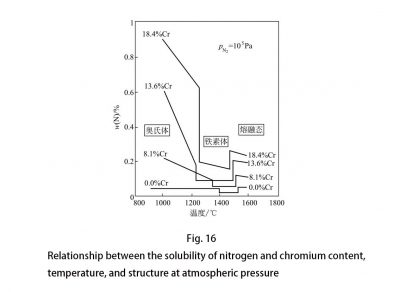
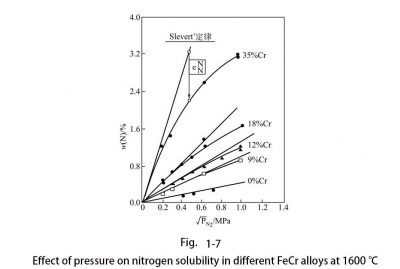
Effect of 1.5 copper on the performance of stainless steel and its weld
Copper is a weaker austenite-forming element, and its ability to form austenite is only 30% of nickel. The solubility of copper in steel is limited by the content of chromium and nickel in steel. Chromium limits the solubility of copper in steel, but nickel increases the solubility of copper in steel. Copper and nickel are completely miscible, while copper is almost insoluble in chromium. Copper has a lower affinity for oxygen than iron. In the process of forming iron scales, copper will be enriched under the formed iron scale layer. This enrichment will lead to the formation of iron-copper low melting eutectics and lead to surface cracks.
In the FeNiCu phase diagram, there are α, γ, and ε phases, and the existence of these phases is related to the composition and temperature of the steel. The presence of the copper-rich ε phase adversely affects the hot workability of stainless steel and even catastrophically deteriorates. To control this adverse effect, the amount of copper in stainless steel should be limited. Generally, the amount of copper in FeCr alloy does not exceed 2% to 3%; the amount of copper in CrNi austenitic stainless steel does not exceed 4%. In martensitic stainless steel and maraging stainless steel, under certain heat treatment conditions, copper can make these two types of stainless steel secondary hardening and age strengthening. Copper also has a significant effect on the cold work hardening rate of austenitic stainless steels. Copper can also increase the hot crack sensitivity of austenitic stainless steels.