Gas Metal Arc Welding (GMAW), or what is commonly referred to as Metal Inert Gas Welding (MIG) and sometimes also referred to as Mechanized Inert Gas, is an automated process in which all three components initiate at the same time once the trigger on the gun is pulled.
The welding can be completely automatic or semiautomatic. When completely automatic, the wire feed, power setting, gas flow and travel over the workpiece are pre-set and function automatically. When semiautomatic, the wire feed, power setting and gas flow are pre-set, but the torch is manually operated. The welder directs the torch over the weld seam, holding the correct arc-to-work distance and speed.
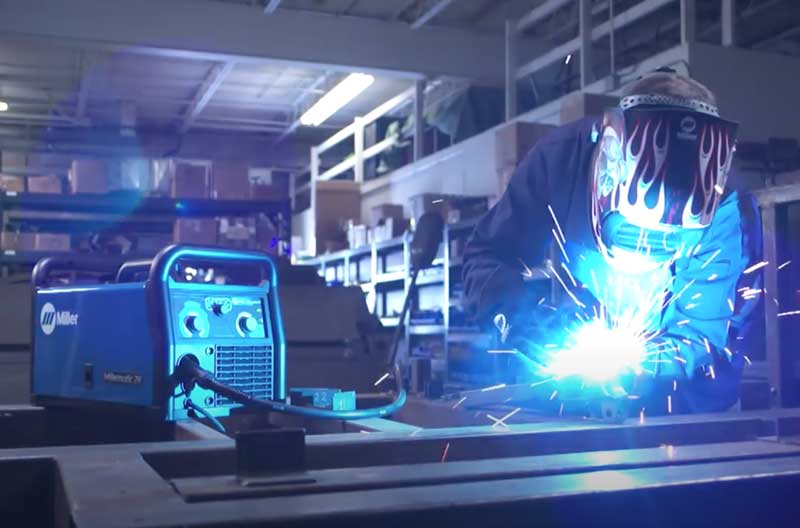
Figure 1 Gas Metal Arc Welding(GMAW) with Millermatic
Basic of GMAW
The metal inert-gas welding ( MIG ) uses a continuous consumable wire electrode. The molten weld puddle is completely covered with a shield of inert gas. The wire electrode is fed through the torch at pre-set controlled speeds. The shielding gas is also fed through the torch.
The filler metal for a MIG welder is a wire that comes on a large spool. Just like in stick welding, the filler metal is also the electrode. The machine has a motor that feeds the wire through a hose to the gun. The power supply that creates the arc is fed through the same hose as the shield gas and wire. A direct current (DC) is most commonly used in MIG welding. A nozzle covers the gun tip where the wire comes out. Under the nozzle are a series of uniform holes that deliver the shielding gas evenly over the arc point. Once the trigger is engaged, all three elements activate simultaneously and feed continuously as long as the trigger is depressed.
The rate at which the wire is fed through the gun and the amount of electricity used is determined by the settings of the machine. You set the voltage and the wire speed in relation to the thickness of the metal to be welded. The shield gas pressure is set using the regulators that are attached to the tanks of gas. The pressure setting for the shield gas is determined by the manufacturer of the machine, normally anywhere between 20 and 30 cubic feet per hour (commonly referred to as CFH). (Note: In countries using metric measurements, the common terminology is cubic meters per hour, or CMH.)
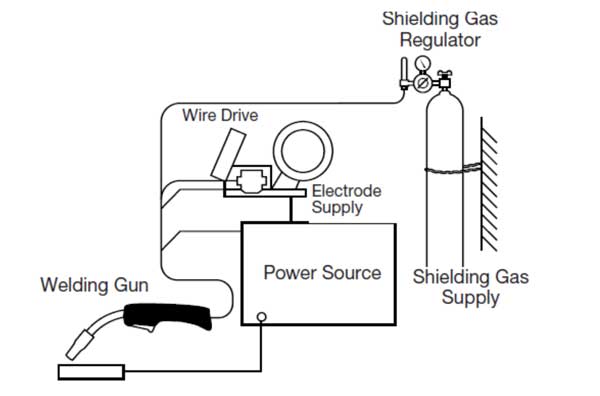
Figure 2 Diagram for Gas Metal Arc Welding
Current for GMAW
Different welding currents have a profound effect on the results obtained in gas metal arc welding. Optimum efficiency is achieved with direct current reverse polarity (DCRP). The heat in this instance is concentrated at the weld puddle and therefore provides deeper penetration at the weld. Furthermore, with DCRP there is greater surface cleaning action which is important in welding metals having heavy surface oxides such as aluminum and magnesium.
Straight polarity (DCSP) is very impractical with MIG welding because weld penetration is wide and shallow, spatter is excessive, and there is no surface cleaning action. The ineffectiveness of straight polarity largely results from the pattern of metal transfer from the electrode to the weld puddle. Whereas in reverse polarity the transfer is in the
form of a fine spray, with straight polarity the transfer is largely of the erratic globular type. The use of AC current is never recommended since the burn-offs are unequal on each half-cycle.
Welding Wire for GMAW
In Gas Metal Arc Welding (GMAW), in order to ensure that the weld has sufficient mechanical properties and does not generate pores, the welding wire must contain more deoxidizing elements such as silicon, manganese, aluminum, or titanium than the base metal. In order to reduce spatter, the carbon content of the welding wire must be limited to less than 0.1%. There are two kinds of copper plating and non-copper plating on the surface of the welding wire. Copper plating can prevent the welding wire from rusting, and can improve the conductivity of the welding wire and improve the stability during the welding process. Stainless steel MIG welding wire does not require copper plating.
ER70s-6 is the most commonly used welding wire. It has better process performance and higher mechanical properties, and is suitable for welding low carbon steel and low alloy steel. ER308 MIG wire, ER309 MIG wire and ER316L MIG wire are commonly used stainless steel welding wire, suitable for Gas Metal Arc welding of most stainless steel.
Deposition Rate with GMAW
Each of the variations has a considerable range of deposition rates based on the weld procedure employed. Figure 3 shows the relationship of deposition rates for the steady current and different electrode sizes used. This chart is based on carbon steel base metals and electrodes. For welding nonferrous metals, deposition rates vary considerably due to the density of the metals.
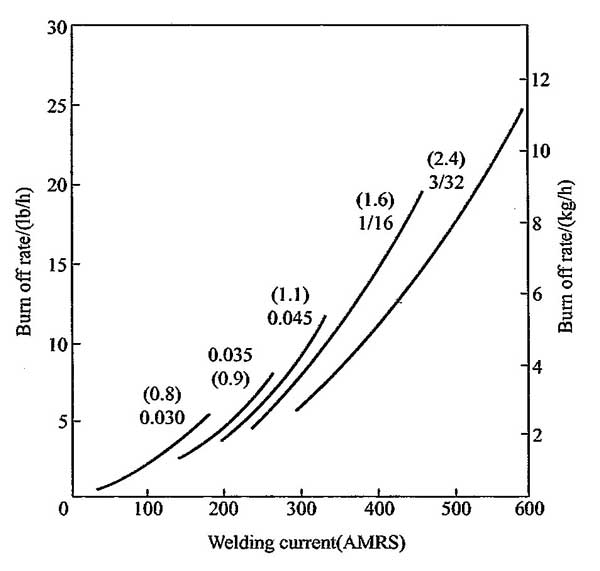
Figure 3 Deposition rates for steady current and different steel electrode size
The deposition rates of gas metal arc welding are higher for the same welding currents than that obtained with shielded metal arc welding. These higher rates occur because there is no electrode coating that must be melted. The current density on the small-diameter electrode wires is much higher than with covered electrodes, which contributes to the higher deposition rates for the same welding current. The tip-to-work distance affects deposition rates, and as the distance is increased, the preheating of the electrode wire contributes to higher deposition rates. Excessive stickout cannot be used without losing the ability to point the electrode wire in the joint accurately.
Quality of Welds with GMAW
Gas Metal Arc Welding(GMAW) is a no-hydrogen or low-hydrogen welding process. There is no hydrogen in the shielding gas atmosphere or in any component involved in making the weld. This is based on the use of welding-grade shielding gas and clean, dry electrodes on clean, dry surfaces.
The quality of welds made with the GMAW process can be extremely high. The quality of the weld deposited depends on the electrode wire, its cleanliness, the cleanliness of the joint, the welding procedure, the welding position, and the skill of the welder.
Certain factors may detract from the quality of the deposited weld metal. One is the possibility of reduced efficiency of the gas-shielding envelope. Breezes in the weld area may blow the shielding gas envelope away and allow the atmosphere to come in contact with the molten pool.
The loss of shielding gas is normally noticed by the welder. This will cause a dirty-appearing weld or will create an unstable welding condition or porosity.
Another factor is impure gas that may contain water vapor, oil, or other impurities. Welding with electrode wire that is dirty, oily, or greasy will contribute to inferior weld deposits. Welding on dirty surfaces — wet, oily, or otherwise will reduce the quality of the weld metal.
Advantages of GMAW
The following are considered to be some of the more important advantages of MIG welding:
( 1 ) Since there is no flux or slag and very little spatter to remove, there is a considerable saving in total welding cost. Generally speaking, weld cleanup is often more costly than actual welding time.
( 2 ) Less time is required to train an operator. As a matter of fact welding operators who are proficient in other welding processes can usually master the technique of MIG welding in a matter of hours. All the operator has to do is to pull the gun trigger and weld. His main concern is to watch the angle of the welding gun and speed of travel.
( 3 ) The welding process is faster especially when compared with metallic arc stick welding. There is no need to start and stop in order to change electrode. As a rule weld failures are often due to the starting and stopping of welding, since this condition induces slag inclusions, cold lapping and crater crack.
( 4 ) Because of the high speed of the MIG process, better metallurgical benefits are imparted to the weld area. With faster travel there is a narrower heat-affected zone and consequently less molecular disarrangement, less grain growth, less heat transfer in the parent metal, and even more important, greatly reduced distortion.
( 5 ) Although originally TIG welding was considered more practical for welding thin sheet, because of its lower current, the development of the short circuiting transfer technique now makes it possible to weld thin stock equally as effectively with the MIG process.
( 6 ) Since MIG welding has deep penetrating characteristics, narrower beveled joint design can be used. Furthermore, the size of fillet welds is reduced by comparison to other welding methods.
Get Notified of New Articles
Leave your email to get our weekly newsletter.